Cutting Edge: Exploring the Latest Innovations in Oxyfuel Cutting Consumables
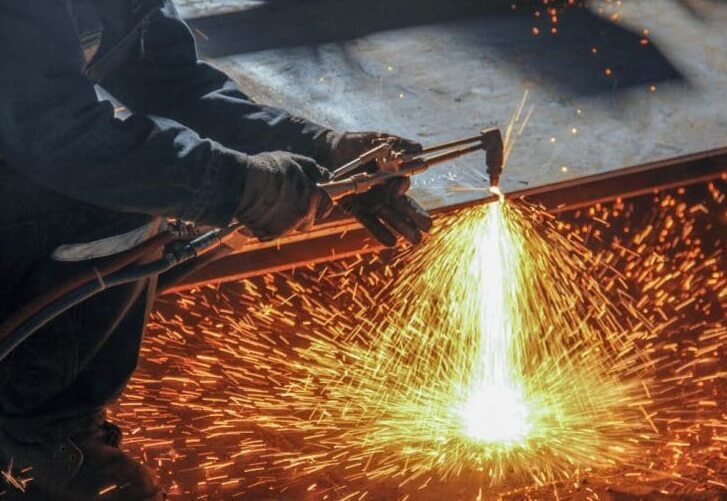
Oxyfuel Cutting
In the article, we can discuss the advancements in cutting tips and nozzles, improvements in durability and wear resistance, and the impact of these innovations on the quality and efficiency of oxyfuel cutting. When it comes to innovations in oxyfuel-cutting consumables, there have been some exciting developments in recent years.
One area of innovation is the improvement of cutting tips and nozzles. Manufacturers have been working on designing tips and nozzles that can provide better heat distribution, a longer lifespan, and more efficient cutting performance. These advancements can result in increased productivity and cost savings. Additionally, we can touch on the potential benefits of alternative cutting methods and their impact on the industry.
Enhanced cutting tips and nozzles
In recent years, manufacturers have been dedicated to designing cutting tips and nozzles that take oxyfuel cutting to the next level. These innovative consumables are engineered to provide better heat distribution, ensuring that the cutting process is more efficient and effective. Additionally, they have a longer lifespan, which means less frequent replacements and reduced downtime. With these advancements, businesses can experience improved cutting performance, increased productivity, and ultimately, better results.
Durability and wear resistance
One of the key focuses of innovation in oxyfuel cutting consumables is enhancing their durability and resistance to wear. These consumables are subjected to extreme conditions during the cutting process, including high temperatures and intense heat.
By developing materials and designs that can withstand these harsh conditions, manufacturers have been able to extend the lifespan of cutting tips and nozzles. This leads to cost savings for businesses as they can minimize the frequency of replacements and reduce the associated downtime.
Improved quality of cut
The design advancements in oxyfuel cutting consumables have also resulted in improved quality of the cut. For example, better gas flow control allows for more precise and consistent cutting, resulting in cleaner edges and reduced post-cutting work.
The enhanced stability during cutting ensures that the consumables maintain their performance, even during prolonged cutting sessions. These improvements contribute to higher-quality cuts, which is crucial for industries that require precise and accurate results.
Increased productivity and cost savings
The innovations in oxyfuel-cutting consumables ultimately lead to increased productivity and cost savings. By utilizing cutting tips and nozzles with improved heat distribution and durability, businesses can optimize their cutting processes, reducing the time required for each cut.
This increased efficiency translates into higher productivity and throughput. Additionally, the longer lifespan of these consumables reduces the need for frequent replacements, saving businesses money on consumable costs and minimizing downtime for maintenance and replacements.
Alternative cutting methods
While oxyfuel cutting remains a popular and widely used method, it’s worth mentioning the potential benefits of alternative cutting methods. Plasma cutting and laser cutting, for example, offer their own unique advantages.
Plasma cutting provides faster cutting speeds and the ability to cut a wider range of materials, while laser cutting offers exceptional precision and the ability to cut intricate shapes. Exploring these alternative methods can open up new possibilities for businesses, allowing them to choose the cutting technique that best suits their specific needs. Read more